Предиктивное ТО и определение коренных причин отказов RCA
В предыдущей статье мы говорили о том, что системное предиктивное ТО является большим достижением в области ТОиР и привносит существенное повышение уровня надежности оборудования. Но это не все. Использование предиктивного менеджмента играет ведущую роль и при определении коренных причин отказов.
В международной практике анализ первопричин отказов носит название RCA (Root cause analysis). Методов и способов проведения RCA огромное количество. Но в целом, всех их можно подвести к стандартному определению. RCA – это любой структурированный подход поиска факторов, приведших к нежелательным последствиям, с целью определить какие действия (бездействие) или условия необходимо изменить, чтобы предотвратить повторение подобных нежелательных последствий.
У лучших методов RCA есть четко определенные процессы. Но зачастую основная причина неправильно используется для описания глубины причинно-следственной цепочки, на которой может быть разумно реализовано вмешательство, чтобы предотвратить нежелательный результат. Другими словами, нам нужно вернуться только к тому событию, в котором можно идентифицировать что-то, что позволяет нам контролировать или предотвращать отказ оборудования.
В основном RCA — это сбор данных или информации. Мы используем эту информацию, чтобы решить, как предотвратить отказ или минимизировать его последствия. Предиктивное ТО – отличный метод для сбора информации. Для иллюстрации воспользуемся неисправностями подшипников. Без хорошего процесса предиктивного ТО отказы подшипников обычно перерастают в катастрофические повреждения. Повреждается не только подшипник, но и ротор, поддерживаемый подшипниками.
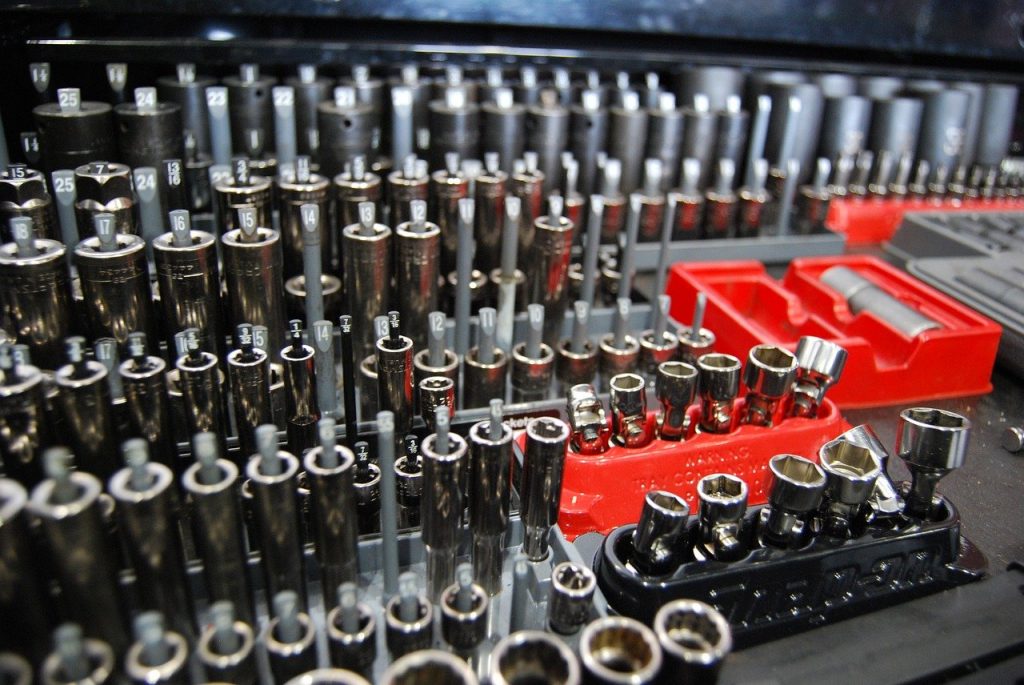
Когда это происходит, бывает трудно увидеть повреждения подшипника и определить причину отказа. Из-за чрезмерного нагрева подшипник может деформироваться до такой степени, что станет похожим на сгусток металла и шлака. То есть, место преступления загрязнено до такой степени, что улики будут утеряны.
Если в этом сценарии инициируется RCA, поиск первопричины может оказаться трудным из-за утерянных доказательств. И разбор превращается в исключительно случайную историю с контрпродуктивными выводами.
А вот если бы подшипник контролировался с помощью непрерывного анализа вибрации, надвигающийся отказ мог быть обнаружен в самом начале его развития, а подшипник был бы выведен из эксплуатации до того, как возникло какое-либо сопутствующее повреждение. Большинство предприятий даже и не стали бы проводить RCA при таком сценарии – достаточно того, что ТОиР предотвратило крупные потери и вовремя все заменило.
Но предположим, что RCA все-таки инициируется (исходя из здравого смысла), чтобы определить причину отказа подшипника. Начинаем задавать вопросы «почему» произошел отказ. RCA в основном предназначена для сбора информации. И в этом сценарии отказа у нас есть неповрежденный подшипник, содержащий улики, а не серый кусок металла и шлака, обнаруженный в предыдущем сценарии.
Подшипник осмотрен, на внешнем кольце видна электрическая канавка. Осматриваемый подшипник — это подшипник электродвигателя, а двигатель заземлен на здание. Заземление здания не функционирует. Почему не функционирует? Персонал знал, что заземление отключено, но его функцию важной не считал. К тому же никто не помнит кто и когда его отключил и проверял ли кто-либо вообще заземлитель в почве. Почему персонал думал, что земля не важна? Они не понимали функции земли и не научены ее обслуживанию. Коренная причина: системой менеджмента ТОиР заземлитель здания не был охвачен: отсутствие планирования, действий, проверок, улучшений (PDCA).
Рассмотренный выше сценарий показывает, насколько ценным может быть предиктивное ТО при проведении RCA. Фактически, когда речь идет об отказах оборудования, предиктивное ТО чаще всего может предоставить нужную информацию для RCA.
Таким образом, предиктивное ТО не только является частью RCM, но и принимает непосредственное участие в RCA.
А. Татьянич
Читать также:
- Управление ремонтами.
- Общие черты и характерные особенности процедуры RCM-анализа.
- Периоды развития систем ТОИР.
- НОВЫЙ УРОВЕНЬ МЕНЕДЖМЕНТА ПРОИЗВОДСТВЕННЫМИ АКТИВАМИ: ИНСТРУМЕНТЫ, МЕТОДЫ, ПОДХОДЫ
- ROI В RCM. НАСКОЛЬКО ВЫГОДНО И МОЖНО ЛИ ОЦЕНИТЬ ПРОЕКТ ДО ВНЕДРЕНИЯ?
- ЗАДАЧИ ПО МОНИТОРИНГУ СОСТОЯНИЯ ОБОРУДОВАНИЯ В RCM